The role of Calcium carbonate in the plastic industry in general and each product industry in particular (such as SPC flooring, PVC pipes, Filler masterbatch…) has been mentioned a lot in news topics. Different industries require separate standards for this CaCO3 input material. In high-class plastic production lines serving the market, manufacturers also set their own standards for calcium carbonate raw materials.
Good chemical stability
Plastic manufacturers will identify a good source of CaC03 material for their business based on its chemical stability. After high-temperature calcination of calcium carbonate, chemical stability is very good, basically not with the various parts of the plastic system chemical reaction, but the surface of the organic modifier may be involved in a chemical reaction.
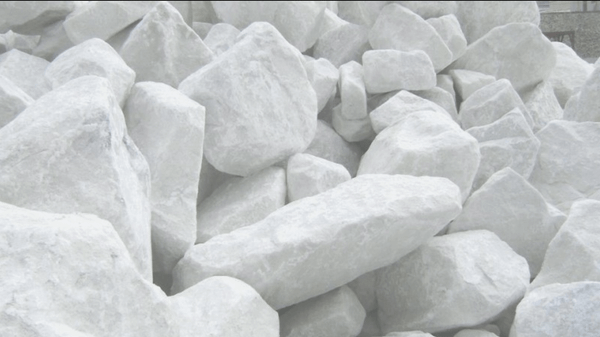
For example, the surface modification of calcium carbonate through acidic substances such as stearic acid and its derivatives, because of the reaction between iron and stearic acid in calcium carbonate, will affect the color of calcium carbonate powder, which is susceptible to yellowing, especially at high temperatures processing of plastics.
Good temperature resistance
The production chain of plastic products is processed in a high-temperature environment (usually greater than 180 ℃), so another requirement of calcium carbonate should be in the heating molding temperature conditions that do not decompose color. Calcium carbonate thermal decomposition temperature of more than 800 ℃ and plastic processing temperature will not exceed 350 ℃, so calcium carbonate itself will not occur thermal decomposition. However, traditional organic modifiers (such as stearic acid, titanate, silane coupling agent) because at high temperature are easy to yellow and decompose, resulting in increased VOC, a lot of calcium carbonate manufacturers in practical applications have encountered the “yellow change” problem or low brightness whiteness.
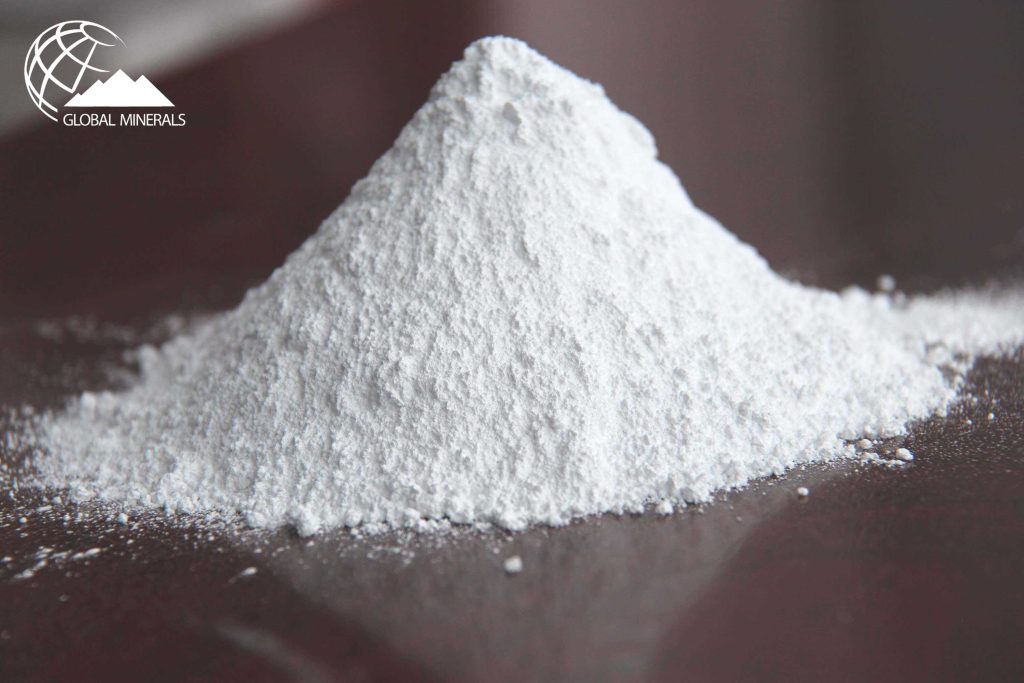
The processing of excellent
The standard “Processing performance” of Calcium carbonate is evaluated by 3 criteria:
Good dispersion
For the filling plastic, uniform dispersion of calcium carbonate particles in the resin mixture is the prerequisite. The smaller the filler particle size, the better the mechanical properties of the filled plastic material when the same proportion is filled. The dispersion of calcium carbonate is mainly affected by intermolecular forces, polarity adsorption, and particle fineness.
Low oil absorption
The lower the oil absorption, the less resin or plasticizer is needed for wetting the equivalent calcium carbonate. For most plastic products such as soft PVC, artificial leather, cable material, etc., it is necessary to use plasticizers to help the plastic system of the mixture be plasticized, the higher the calcium carbonate oil absorption value, the better the quality. The plasticizer is more easily adsorbed to the filler, so it loses the role of the plasticizer. In order to make the resin system mixture achieve a certain degree of softness, it is necessary to increase the amount of plasticizer which leads to an increase in cost. By changing the surface of calcium carbonate, the surface of calcium carbonate particles can be organically coated, and the oil absorption value will be greatly reduced.
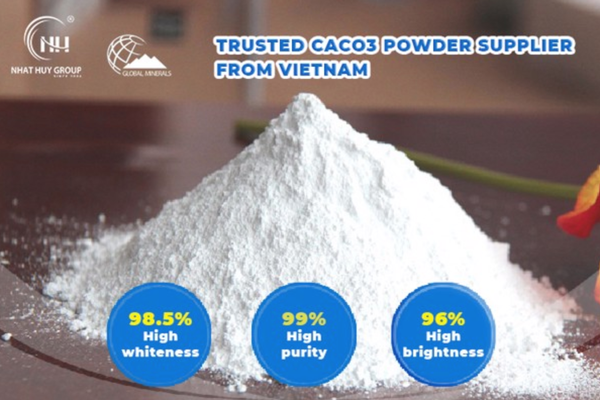
Hydrophobic Good
Calcium carbonate is a very hygroscopic substance and very easy to absorb moisture, once in the storage process or the process of absorbing moisture is not good at CaC03 factories, it will cause the following problems:
(1) Calcium carbonate caking, the fluidity of the dry powder is easy to clog the sieve hole, leading to difficulty in adding;
(2) In addition, when the plastic product is molded at a high temperature, due to water vapor precipitation, the product “bulges” or “holes” and other defects, which seriously affect the appearance of the plastic product and the strength of physical durability.
Hi, this is a comment.
To get started with moderating, editing, and deleting comments, please visit the Comments screen in the dashboard.
Commenter avatars come from Gravatar.